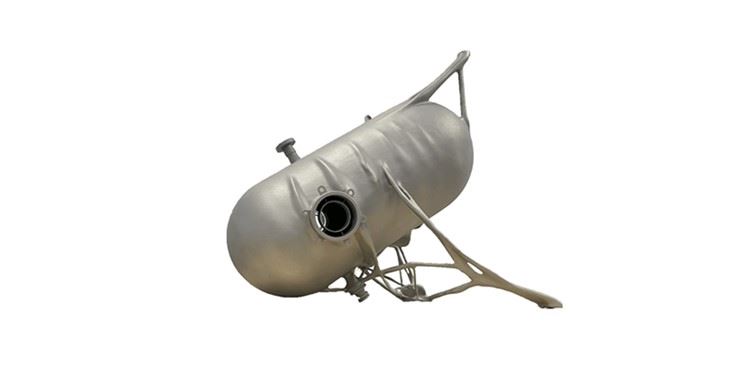
헥사곤 매뉴팩처링 인텔리전스는 니콘 SLM 솔루션즈와 적층제조(AM) 기술의 설계 자유도를 활용해 대형 항공기 연료 시스템 부품을 재설계하는데 협력했다고 발표했다.
헥사곤은 자사의 적층제조 설계(DfAM : Design for Additive Manufacturing) 설루션과 니콘 SLM 솔루션즈의 멀티 레이저 금속 적층제조 기술을 결합해, 부품을 통합하고 75%의 경량화 및 정밀한 기하학적 공차를 달성했다고 전했다. 에어버스 오퍼레이션(Airbus Operations)은 이 기술을 활용해 A330 기종의 보조 동력 장치(APU)에 연료를 공급하는 연료-공기 분리기를 재설계했다. 그 결과, 더 단순하고 효율적인 A330 연료-공기 분리기 시제품 생산에 성공해, 35kg이던 기존의 연료 공기 분리기를 8.8kg 미만으로 줄여 약 75%의 경량화를 달성했다.
연료 공기 분리기는 APU 연료 공급 시스템에서 공기를 제거해서 주 엔진이 꺼져 있을 때 APU가 필수 항공기 시스템에 전원을 공급할 수 있도록 하는 부품이다. 기존 부품은 30개 이상의 개별 부품으로 제작되어 노동 집약적인 수동 용접 및 조립을 거쳐 긴 리드 타임이 발생해 설계 개선이 제한적이었다. 에어버스 오퍼레이션과 니콘 SLM 솔루션즈는 공기 분리기의 생산성과 성능을 최적화하기 위해, 니콘 SLM 솔루션즈의 대형 멀티 레이저 3D 프린터 ‘NXG XII 600 시스템’을 활용했다. 이를 기반으로 제조 과정을 단순화하고 리드타임 단축으로 설치를 간소화하는 프로세스를 개발했다.
이를 위해 헥사곤의 적층제조 설계 워크플로를 도입해 30개 이상의 부품을 단일 경량 부품으로 통합했으며, 경량 설계 최적화 설루션 소프트웨어인 MSC 에이펙스 제너레이티브 디자인(MSC Apex Generative Design), 적층제조 설루션인 AM 스튜디오(AM Studio), 금속 가공 및 제조공정 시뮬레이션 소프트웨어인 시뮤팩트(Simufact)를 통해 정밀한 공차 관리 및 제조 단순화, 리드 타임 감소, 설치 간소화 프로세스를 구축했다.
헥사곤은 “이번 협력으로 부품 무게가 크게 줄어 제조 시간과 공정이 간소화되고, 항공기의 연료 효율이 높아졌다”면서, “에어버스는 이 기술을 향후 항공기 설계에 널리 적용할 수 있는 유리한 위치를 확보하고 있다”고 소개했다.